Rotational molding, often hailed among the most functional developing methods, provides all sorts of advantages across a variety of market sectors. From its versatility in style to its expense-usefulness and eco-friendliness, rotational molding has established itself as being a desired method for developing a wide array of goods. Let's explore the benefits of Rotational Molding along with its relevance in modern developing.

1. Design and style Freedom:
Certainly one of the major advantages of rotational molding is its unequalled layout flexibility. As opposed to typical manufacturing techniques like injections molding, which in turn demand sophisticated and dear molds, rotational molding provides for the introduction of elaborate designs and designs with family member simplicity. This versatility in layout permits producers to produce highly customized goods customized to particular needs, giving them a competitive edge in the marketplace.
2. Charge-Effectiveness:
Rotational molding gives substantial financial savings in comparison to other developing functions. Because it doesn't require the usage of intricate molds or tooling, the preliminary setup expenses are relatively low. Furthermore, rotational molding employs unprocessed resources effectively, reducing waste and reducing fabric charges. The approach also makes it possible for the manufacturing of sizeable, hollow components in just one operations, getting rid of the requirement for additional construction processes and additional leading to cost-performance.
3. Toughness and Energy:
Merchandise produced through rotational molding are recognized for extraordinary sturdiness and power. By evenly releasing substance throughout the mold and making use of managed heating and air conditioning periods, rotational molding produces goods with standard wall structure density and ideal structural sincerity. This will make rotational shaped elements proof against affect, corrosion, and tough enviromentally friendly situations, making certain long life and stability in different apps.
4. Substance Adaptability:
Rotational molding is compatible with a variety of resources, which includes polyethylene, Pvc material, nylon, and polypropylene, and the like. This flexibility allows companies to pick the the most appropriate fabric for their specific app, whether or not it requires compound opposition, Ultraviolet stableness, or compliance with food-grade criteria. Moreover, rotational molding can combine additives and reinforcements to help increase materials properties and gratification.
5. Sustainability:
In today's environmentally conscious entire world, rotational molding stands out for an eco-warm and friendly production process. As opposed to some traditional methods that produce unwanted squander or eat significant amounts of energy, rotational molding generates minimal scrap and uses relatively low stamina. Furthermore, the recyclability of rotational molded goods plays a role in a circular economic climate, decreasing the environment footprint linked to producing and disposal.
6. Scalability:
Rotational molding is extremely scalable, which makes it ideal for both tiny-scale and huge-scale manufacturing goes. Whether or not producing a individual prototype or 1000s of devices, manufacturers can certainly adapt generation volumes to fulfill desire without diminishing top quality or performance. This scalability tends to make rotational molding an excellent choice for companies looking to ramp up production or expose new services to the industry rapidly.
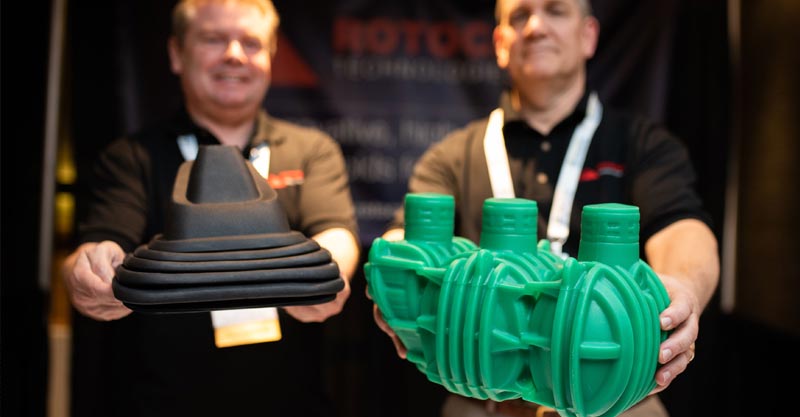
In conclusion, the great things about rotational molding are diverse and far-getting to, so that it is a preferred choice for suppliers across a wide range of businesses. From the style freedom and cost-performance to its sturdiness, material overall flexibility, sustainability, and scalability, rotational molding consistently push creativity and condition the way forward for production.